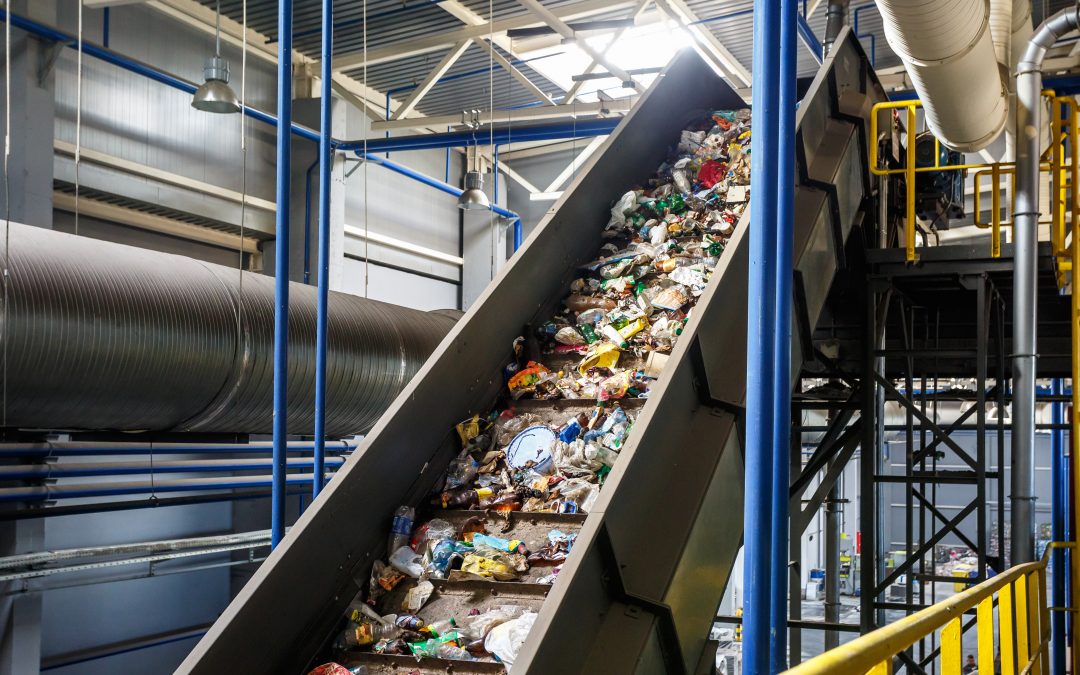
What Parts do we Ultrasonic Clean for Plastic Recyclers?
Typically the parts we ultrasonic clean for plastic recyclers are the filters, the heat exchangers, the print rollers and other precision-engineered parts that have small holes or internal cavities that require cleaning. They are difficult, if not impossible, to clean through conventional jet washing, soak or other abrasive methods. They also tend to have small particulate contamination and are expensive to replace.
Let’s look at each in turn;
Oil filters from hydraulic or lubrication systems for fast-moving parts.
Filters – these come in all shapes, sizes and function but the most common filters in plastic recycling are;
- Laser disc filters, or hot melt filters, used to filter remaining contamination from the plastic being treated;
- Extraction filters used to keep the work environment free of dust, oil and other airborne contaminants;
- Oil filters from hydraulic or lubrication systems for fast-moving parts.
Ultrasonic cleaning with the right chemistry for the relevant contaminant is ideal to remove small particulate from small openings and internal cavities typical of filters.
Heat exchangers – Most machines that work under high pressures and/or for long periods reach temperatures above their optimal working conditions and therefore require some form of cooling. This is done via heat exchangers, sometimes water-based, sometimes oil-based or even air-based coolers. By their very nature, the cooling media will create and then deposit particulate matter within the cooling mechanism. Over time this will reduce its effectiveness until it no longer performs its function. The removal of this contaminant is essential for it to continue doing its job. Ultrasonic cleaning reaches all surface areas of the part submerged in the cleaning solution, including internal cavities. With the right chemistry, any type of contaminant can be removed, from scale and rust to carbon and solidified oils.
Print Rollers – A lot of plastic is essentially packaging and therefore is ultimately printed upon to identify its contents or promote its producer. Many plastic recyclers offer some printing on the plastics they manufacture from recycled product. And this printing process on packaging material often users print rollers to carry the ink. These rollers are precision engineered to carry precise volumes of the ink but over time get dirty and cannot carry the necessary volumes of ink for good print quality. Ultrasonic cleaning is a well-proven method for restoring these rollers to full volume and optimal print quality.
All the parts mentioned above share common features. They are commonly highly engineered, high performance, high value and highly critical to the overall process of recycling plastic and converting to the desired end product. The alternative to ultrasonic cleaning is either replacement or highly laborious and time consuming manual cleaning that is usually only partially or temporarily effective.
If this sounds familiar because you either have the parts mentioned above or you have another cleaning issue then the chances are we can help, saving you time and money, improving the quality of your end product, and reducing your stress levels. Just get in touch and we’ll be happy to discuss your options, how we can help, and offer you a free trial clean to prove it will work for you.
For a free trial clean, a no-obligation discussion, or even a visit when the current situation permits, just call us on 01924 495 975 or e-mail Andrew on andrew@sonicsolutionsltd.com