Industrial Parts Cleaning for the Plastics Industry
Save you & your team time, hassle & money by getting your industrial parts cleaned to the highest possible standards using the latest industrial cleaning techniques, reducing downtime and eliminating excess spend on consumables.
Annual Savings of at least £75,328
“All in all a massive win for us, reducing costs and increasing revenue simultaneously in a very competitive market.”
Simon - Engineering Support Manager
Berry BPI Group
How we saved Simon £75,328 - Simon’s calculations were based on the following;
- An average 13 filters a month were cleaned in 2019. Erema laser discs in Simon’s case, but this process also applies to Ettlinger, MAS or other hot melt filters.
- Our multi-stage cleaning process means that each filter now lasts at least twice as long as they would’ve done otherwise
- Any hot melt filter costs well in excess of £1,000
- Total cost of cleaning, carriage, packing etc.. costs in the region of £100 per filter.
Simon’s conservative calculation of an annual saving of £75,328 was based purely on replacement costs. He also benefited from higher throughput, longer runtime and less downtime.
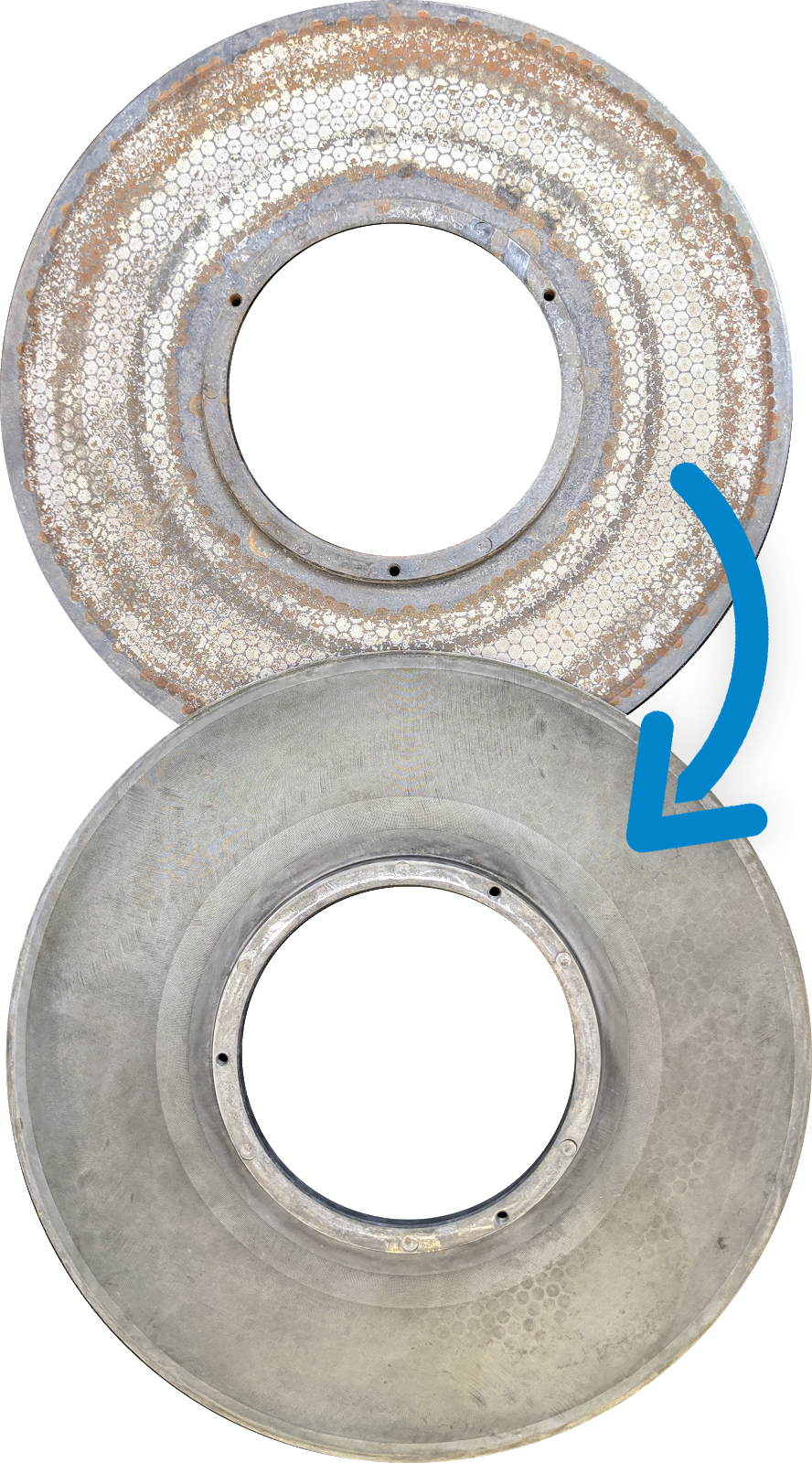
How our full industrial parts cleaning system & expertise benefits the plastics industry
The plastics industry is one of the biggest in the world and depends heavily on machinery and equipment for it’s production. It is critical that this equipment is kept running smoothly, and one of the most effective solutions for a well-running machine is to keep its industrial parts & components clean. Cleaning these industrial parts & components takes precision and expertise, and with the right techniques, you can improve productivity, reduce downtime, and eliminate excess costs for replacement parts.
The manufacturing process of plastics depends on many industrial parts, and each poses its own issues if not properly cleaned. Remove grease, scale, rust, inks, oils, carbon and much more using one, some or all of the following… Ultrasonic Cleaning, Pyrolysis & Thermal Stripping, Jet Washing & Vapour Blasting. If you are still losing time, money, and business through dirt then we should talk.
Why is cleaning your dirty industrial parts better than replacing them?
Parts We Clean for the Plastics Industry
Laser Filters
Various types of laser filters are used in the plastic recycling industry, including Erema, MAS, FIMIC, and Ettlinger laser filters, all used to remove contaminants from plastic recycling processes. Unlike the disposable wire mesh filters that need constantly changing, “continuous melt” filtration uses blades to skim off the majority of contaminants that hit the filter.
Sintered Filters
Sintered filters are used in the production of blown moulding to keep contaminants out of the end product by purifying air before the moulding process. Over time these become trapped with particulate and must be cleaned or replaced. The slow build-up of particulate raises pressures in the system and can lead to major problems.
Heat Exchangers
The air heat exchangers keep the blow moulding air at a constant temperature, meaning products such as plastic bottles are manufactured in an identical and repeatable way. Over time these air heat exchangers gather up deposits from the heating of plastic that leave a sticky layer on the surface, reducing the effectiveness of the equipment.
Condensers
Condensers used in the production of blown moulded products are designed to catch and remove the volatile vapours released in the heating of plastics in the extrusion stage. Over time this sticky “wax” builds up reducing the effectiveness of the “cooler”.
Dust Filters
Dust filters are found in a number of different areas of the plastics industry. In recycling they are used in the grinding process to catch airborne particulate that could affect the health and safety of the workforce and contaminate products. When producing blown film, it’s imperative no airborne particulate is present, so extraction is key.
Pelletising Heads
Pelletising heads are usually cleaned when switching products or if there has been a failure in the filtration process allowing contaminants to block the fine holes. Being that this equipment is almost the last stage of production the tolerances are extremely important and must be kept clean for best results.
Common Problems in the Plastics Industry
Contaminated Extraction System Filters
Extraction system filters and condensers can become contaminated with wax and oil deposits when the use of heat is implemented in the drying of material after the washing and separation processes. These filters and condensers can be extremely expensive to replace and are also very challenging to clean thoroughly.
Restricted Air Flow
To compensate for the restricted air flow, pressures and flow rates are increased. This raises further issues of safety as pressures rise to potentially dangerous levels, and process control reduces as the flow rate increases.
Costly Replacement Parts
Cleaning or replacement of these dirty parts is inevitable at some stage. However not only can these parts be extremely expensive, but they are often bespoke, manufactured abroad and on extremely long lead times, making their replacement a financial, logistical and production nightmare.
Potential Shutdown
Shutdown is an inevitable consequence if the accumulation of residual contaminant is not properly addressed.
Parts Cleaning or Replacement
Quality suffers as control reduces and solid particulate risks being introduced into the end product.
Reduction of Product Quality
To add to the problems, the price of replacement parts is increasing at an exponential rate in many cases.
How We Clean Parts for the Plastics Industry
The Sonic Solution
Contact us
Click onPress the button to open our enquiry form and we’ll come back to you ASAP (usually within the hour) with answers, options, prices and services or call us today on 01924 495 975
Get In Touch
Fill out the form below, or if you would prefer you can call us on 01924 495 975
or email us at hello@sonicsolutionsltd.com
Don’t Spend Another Penny on Replacing or Cleaning Parts Until You’ve Asked These 7 Critical Questions.
Asking These Questions Saved One Customer over £70,000 a Year, Seriously!
What Cleaning Process Do I Need? A Quick & Easy Reference Guide...
Use this quick reference guide to compare parts vs contaminants to shortlist possible cleaning processes (Ultrasonics vs Pyrolysis vs Jet Wash vs Vapour Blast vs Soak)
The Ultimate Guide to Industrial Ultrasonic Cleaning
Get a complete understanding of the underlying science, equipment and characteristics of ultrasonic cleaning.
Our Story
Hi. I’m Andy, owner of Sonic Solutions for 14 years. Our aim is simple, to get your dirty parts clean, as efficiently and effectively as possible, so you can get on with your business.
We provide a cleaning service, cleaning chemicals, and ultrasonic cleaning equipment, so whether you want to do the job in-house or just let someone else sort it out we can help.
So if you require any cleaning of your equipment to help maintain your parts, increase production and reduce money loss, why not get in touch with our friendly and professional team.
We look forward to hearing from you.
- Andy