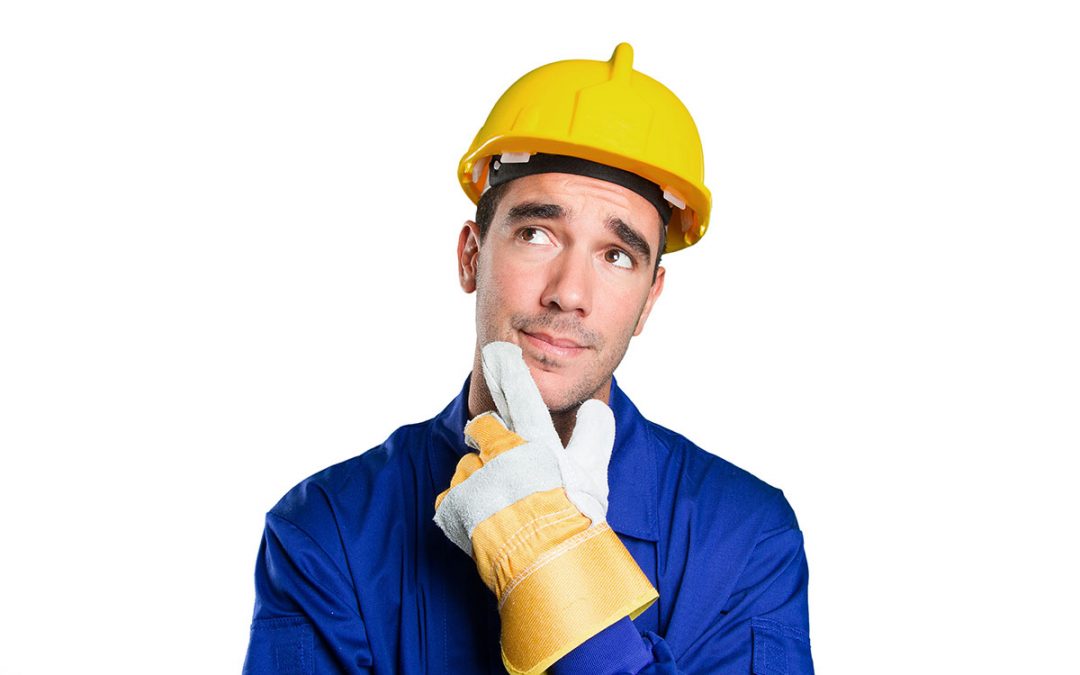
Ultrasonic Cleaning vs Jet Washing for Precision Engineers
Jet blast cleaning is the process of using a high-pressure water pump to generate a flow of pressurised solution (up to 40,000psi) which is passed through a small diameter orifice to form a coherent stream of pressurised fluid. This jet of solution is then directly applied to any objects to be cleaned. The solution is usually water based, often containing a chemical to assist in removing the contaminant, and may also be heated to further assist the cleaning process.
Ultrasonic Cleaning uses the varying pressures created by high frequency sound (greater than 20Khz) as it passes through solution to create and then implode tiny vacuum bubbles (1-200 microns). The force exerted by these implosions (up to 20,000 psi) are intense over a small area, removing particulate adhering to any item submerged in the solution.
What can it clean?
It can be used to clean a wide variety of items relatively quickly and easily. Generally, it can be used to clean any accessible surface that can withstand the high-water pressures. Traditionally used for cleaning volumes of items with straightforward surface geometry and loose oil and particulate, it is used widely in precision engineering for the removal of cutting oils and swarf after machining.
Pros of ultrasonics over jet wash
- By its nature ultrasonics cleans all surfaces which the solution touches, offering a universal clean to any item, irrespective of its surface geometry. In contrast jet washing only cleans the surface under the jet so internal chambers, and inaccessible surfaces, or surfaces with uneven geometry, are impossible to clean to a very high standard with this method. This shortcoming has been addressed by the use of sensor robotics within the cleaning process to hold the item and move it and the jet nozzle to expose all surfaces to the jet stream. Companies such as MecWash have developed some extremely sophisticated machines to overcome this shortcoming. The price of this complexity in both financial and time aspects is considerable however.
- Ultrasonics uses a fixed amount of water in the cleaning bath which can be recycled and filtered to last a considerable period. Jet washing uses large volumes of water which can become waste (up to 1500 Litres per minute), although most modern jet wash units filter and recycle the waste solution to a certain extent.
- High pressures used by jet wash systems can damage delicate and light objects which move about when hit by high-pressure jets. In contrast, the forces created by ultrasonics suck dirt away from the item so do not move it around with the consequent potential for damage.
- Ultrasonics can achieve extremely high levels of cleanliness since they function at the micron level. The microscopic bubbles created in the liquid medium grow to a maximum size proportional to the ultrasonic frequency. At 20 kHz the bubble size is roughly 150 microns in diameter, reducing to 100 microns at 30 kHz and 38 microns at 80 kHz.
- Ultrasonics removes dirt from the surface into the solution, rather than just blasting from the surface. Where dirt eventually lands in a jet wash process is uncertain, and some residue is merely moved from one part of the surface onto another.
- Ultrasonic cleaning is more flexible and adaptable being able to use different solutions to remove a wide variety of contaminants ranging from oils to scale and rust. By contrast jet washing is almost invariably used to remove oils, loose particulate, inks and paints. It is not generally successful in removing scales and rusts where an acid-based solution can be used with ultrasonics.
Pros of jet wash over ultrasonics
- Jet washing can remove large volumes of tough grime, both wet and dried. With a recirculating and filtered system, large quantities of dirt can be effectively removed from items. Ultrasonic solutions can be filtered and recycled but large volumes of dirt put into the solution will diminish the effectiveness and efficiency
- Jet washing can be used safely in potentially volatile environments/situations, since it is invariably within a contained unit.
- Jet washing is fast and economic to clean large volumes of parts. Where the objective is to make parts safe to handle for the next process by removing the majority of oils and swarf rather than cleaning to a reliable high standard, jet washing is more economic than ultrasonics.
Conclusion
Ultrasonic Cleaning is probably the preferred cleaning methodology where parts to be cleaned have the following characteristics;
- Uneven surface geometry with internal chambers and small apertures;
- A high level of cleanliness is required. Where parts undergo further processes, or are a component of a part being used in a very demanding application, then the level of cleanliness required is likely to be higher than jet washing can achieve.
- Small numbers of variable parts are required, so ultrasonic immersion works far better than jet washing.
- Where the contaminant to be removed is more than a simple particulate and oil.
- The volume of dirt to be removed is relatively low, so the cleaning solution does not become too contaminated, too quickly. A pre-wash and filtration can overcome this but adds cost and complexity.
- Items to be cleaned are small, light and delicate so need a gentle cleaning process to prevent damage.
- Jet washing is probably the preferred cleaning methodology where parts to be cleaned have the following characteristics;
- Regular outward facing surfaces to be cleaned (no small holes or internal chambers);
- Large volumes of dirt to be removed;
- Large volumes of items to be cleaned;
- Lower cleanliness levels required;
- Items are heavy and robust enough to not be damaged by high pressure blasting.