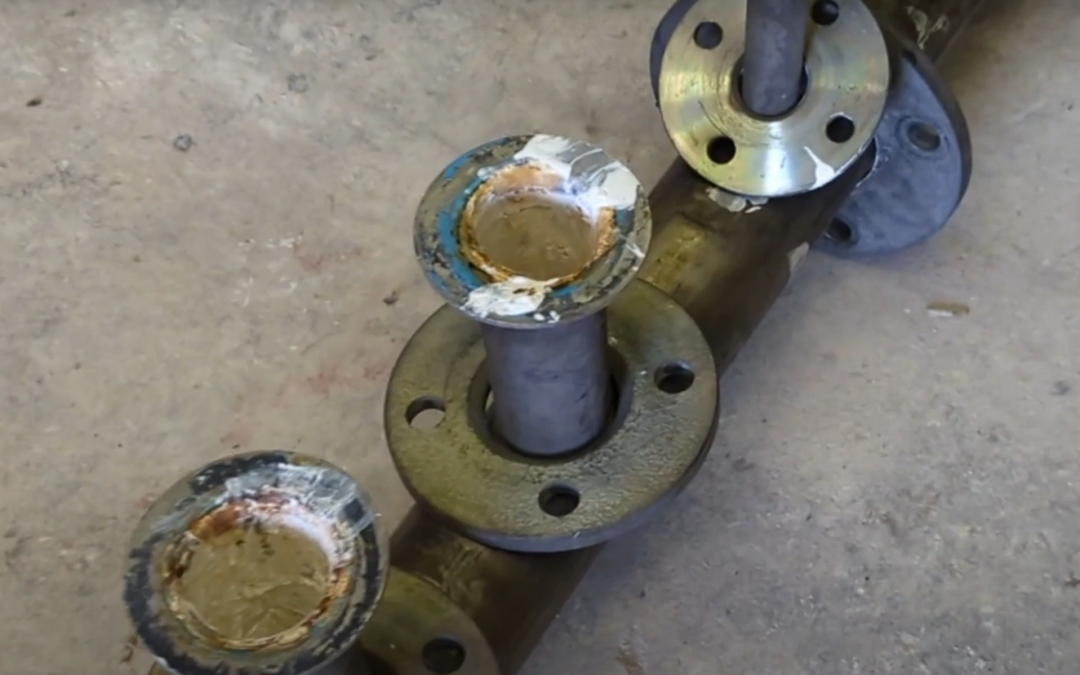
Pyrolysis Parts Cleaning For The Paint Industry
Keeping industrial parts cleaned to the highest standards means your business can save time, hassle, and money. With the right cleaning techniques, you can eliminate excess spend on consumables, reduce downtime and improve both productivity and quality. At Sonic Solutions, we are specialists in cleaning key parts and machinery in the paint industry and we’ve put together this expert guide to handling paint contamination and the solutions available.
The Paint Contamination Problem
Manufacturing paint and polymer coatings involves many different parts, including pipework, nozzles, valves, mixing vessels, filters, conveyor belts, receptacles, and jigs. All of these parts will get dirty with time, as paint residue collects and accumulates on their surfaces. This accumulation of paint and polymer residue causes numerous problems and issues in production, quality, and finance. Some of the most common issues we see caused by this build up are:
- The passage of the product or part can quickly become restricted, slowing throughput unless flow rates are increased.
- To compensate for restricted flow, pressures and flow rates must be increased. In turn, this raises further issues of safety as pressures rise to potentially dangerous levels, and process control reduces as the flow rate increases.
- As control reduces it means that quality begins to suffer, and solid particulate risks are introduced into the end product.
- Any build up of organic material in the process risks the development of bacteria, which is both a health and a quality issue.
- If the accumulation of residual product is not properly addressed and resolved, then it will lead to a complete shutdown of equipment.
It is inevitable that cleaning or replacement of these dirty parts will need to take place at some stage. However, not only can these parts be extremely expensive, but they are also often bespoke, manufactured abroad and on extremely long lead times, making their replacement a financial, logistical and production nightmare.
Ultimately parts need to be cleaned, can you do this in-house?
The short answer is yes and the majority of businesses will look to clean parts themselves as the first option, especially if the cost of replacement is high or the lead time on replacement is long. It might seem like the perfect solution, but in house parts cleaning operations are often not as simple and painless as people think. The problems and pains of in-house cleaning are plentiful, including;
- Cleaning these parts is often a multi-stage process, employing a range of cleaning methodologies, equipment, and chemistry. To take on such cleaning in-house would require significant investment in both equipment and experienced personnel, together with making the space and services available to accommodate the additional process.
- Each different part has different cleaning requirements, and these variable needs make the process even more challenging for an in-house team. Some parts require simple cleaning, while others need a more complex procedure to keep them running well.
- Setting up and running a cleaning facility is usually outside the experience of most production personnel, with the result being that the cleaning results they deliver are disappointing.
Outsourced Parts Cleaning For The Paint Industry
A sub-contracted cleaning operation, particularly when part of a planned maintenance programme, can be extremely effective in both time and money compared to the alternatives of replacement parts or in-house cleaning. Paint can be removed by a number of methods, including pyrolysis (also known as burn-off), chemical stripping (usually either solvent based or highly caustic), or media blasting (using sand, glass, a metallic oxide or soda crystals, either in dry form or within a water jet).
- Pyrolysis: This method essentially burns off the paint from the parts. It Involves gradual heating of the part in an oxygen deprived environment to reduce the paint or polymer to an inert ash, the volatile hydrocarbon elements evaporating and reducing to carbon dioxide and water.
Harder metals like steel and copper will not be adversely affected by this and there is complete removal of the contaminant with only inert residual ash being left. This can then be removed using jet washing and/or ultrasonic cleaning.
Metals may be discoloured by exposure to high temperatures, although their physical and chemical properties are unlikely to be adversely affected by this. Of course, if there are a variety of metals within a part, or some non-metallic attachment like seals, linings and electrical components these may be damaged by the process.
- Chemical Stripping: Most paints can be removed by either solvents or caustic based solutions. Through a combination of dissolving and lifting the paint from the metallic surface they can remove paints and polymers satisfactorily.
However, most modern paints are designed to be relatively resistant to water and common day chemical substances so increasingly strong and aggressive chemistry is needed to remove them. This has clear implications for their handling and usage, with special precautions and procedures required to comply with health and safety regulations. This often creates issues within the process plant itself where the necessary chemical cleaning regime conflicts with the core production process.
- Media Blasting: Blasting small particles at high velocity and pressure is a popular way of removing paints from a hard surface. The media used can vary from silica, sand, metallic oxides, glass beads, baking powder, or dry ice/frozen carbon dioxide pellets. The media will be chosen to be aggressive enough to remove the paint coating but without damaging the underlying material. It may be applied “dry” propelled by compressed air, or “wet” carried within a waterjet.
This is a hard call, especially as paints become more durable, requiring ever greater force to remove. The other big issue with media blasting is actually reaching all the surfaces that require cleaning. Complex geometry and internal openings and channels often mean the contaminating paint cannot be fully removed.
At Sonic Solutions, we offer all the above cleaning solutions. For the removal of paint, our specialists’ preferred method would usually be pyrolysis, unless there is a specific reason not to. Done correctly it removes all contaminating paint without damaging the item itself, leaving the bare metal for any future process.
It should be added that the majority of the time, the burning is only the first stage of the complete cleaning process, usually followed by a combination of jet washing, ultrasonic cleaning or even a further media blast, to leave a completely clean metal surface. At Sonic Solutions, we are able to offer a unique cleaning process compared to both in-house cleaning and other subcontract cleaning operations as we use a variety of cleaning processes to achieve the desired level of cleanliness.
Our cleaning expertise and experience combined with our flexibility and desire to deliver what the customer wants, when they want it, explains why some of the biggest and most demanding paint manufacturers like PPG, Dow, and Dupont rely on us to get rid of their unwanted paint residue from working parts.
To see how the process works, watch us in action.
At Sonic Solutions, we are experts in industrial parts cleaning and we are here to help! We are more than happy to explore, advise and assist with whichever option works best for you and can offer hire or finance options. Contact our expert team today to discuss your requirements in more detail.