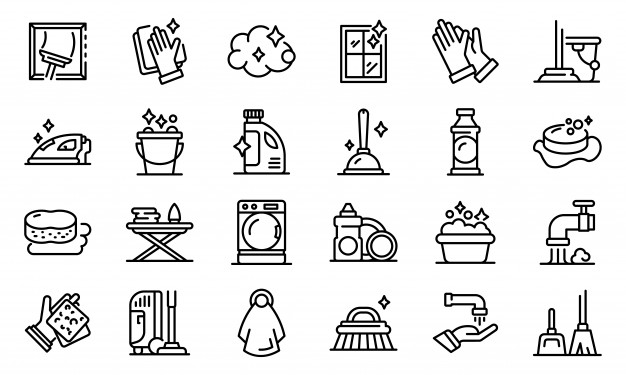
This article explores 5 alternative cleaning methods to ultrasonic cleaning, Jet Washing, Vapour Blasting, Media Blasting, Chemical Cleaning & Electro-cleaning. I’ll talk about what each cleaning method is, how it works and take a look at the pro’s and cons of each.
Jet Washing
What is it?
Jet blast cleaning is the process of forcibly propelling a high pressure (up to 40,000psi) stream of liquid at a surface to remove contaminants. The solution is usually water based, often containing a chemical to assist in removing the contaminant, and may also be heated to further assist the cleaning process.
How does it work?
A high-pressure water pump generates a flow of pressurised solution which is passed through a small diameter orifice to form a coherent stream of pressurised fluid. This jet of solution is then directly applied to any objects to be cleaned.
What can it clean?
It can be used to clean precipitators, condensers, evaporators, clinkers, air pre-heaters, kilns, stacks, dryers, boilers, tube bundles, tanks, reactors, sewers and drains, process piping and outer surfaces. Generally, it can be used to clean any accessible surface that can withstand the high-water pressures.
Pros?
Can remove tough grime.
Can be used safely in potentially volatile environments/situations, since it is invariably within a contained unit.
Fast to clean large areas.
Cons?
Uses large volumes of water which can become waste (up to 1500 Litres per minute), although most modern jet wash units filter and recycle the waste solution.
High pressures can damage delicate objects.
Only cleans the surface under the jet so internal chambers, and inaccessible surfaces, or surfaces with uneven geometry, are impossible to clean to any real standard with this method.
Comparisons:
Cheaper than media blasting.
More abrasive than ultrasonic cleaning.
[1] https://jetblast.net/water-jet-blasting/
[2] https://www.omax.com/learn/how-does-waterjet-work
Vapour Blasting
What is it?
Vapour blasting is a cleaning process in which an abrasive material (e.g. tiny glass beads) is mixed into water. This waterborne media is then forced into a high-pressure stream and directed at a surface in order to remove grime.
How does it work?
A purpose designed pump forces water and the abrasive media into a high-pressure slurry which is projected in a stream towards the object being cleaned. The abrasive media removes contaminant from the surface being cleaned whilst the water washes both the contaminant and the media away. This process is usually done within a blast cabinet to contain the waterborne media and prevent the accidental abrasion of other materials near the cleaning process.
What can it clean?
It is used; in the automotive industry for surface finishing; for cleaning dies and moulds; for removing paint, rust and carbon in the engineering industry; finishing of steel surfaces (and similar materials); cleaning PCB’s and electrical connectors and removing small burrs from components after their manufacture.
Pros?
The water means the abrasive media is less aggressive on the object being cleaned.
The abrasive material effectively removes a large range of tough contaminants like rust, paint, and carbon.
Strong cleaning power.
Produces a very even polished finish on items being cleaned
Cons?
Produces large volumes of contaminated waste water.
Only useful on hard, solid contaminants
Items being cleaned are left with residual media, which may well need further cleaning to remove.
Can damage delicate materials.
Cannot clean internal chambers as only the area directly under the jet is cleaned.
Comparisons:
Produces less dust than dry blasting.
More abrasive (and potentially damaging) than ultrasonic cleaning.
[3]https://www.vixen.co.uk/wet-blasting/what-wetblasting-guide-vapor-blasting-process
Media Blasting
What is it?
Media blasting is a process in which a stream of air is accelerated towards an object to remove its surface. The air contains tiny pieces of a solid media which remove the layer as they collide with the object. The most commonly known variant is sandblasting, although real sand is no longer used due to the health issues related to the inhalation of silica particles.
How does it work?
Pressurised air carries small bits of material to hit a surface, these tiny pieces hit the surface of the object with adequate force to remove the outermost layer. Common media used in this cleaning process are plastic beads, ground-up walnut shells, glass beads and pieces of aluminium oxide.
What can it clean?
Media blasting is most commonly used to remove layers of rust or old paint but it can also be used for removing layers of other hard contaminants such as calcium deposits. Equipment can be purchased for home-use (e.g. for stripping bike frames or metal outdoor furniture).
Pros?
One of the least expensive cleaning processes with cleaning equipment typically in the range of £200-£1500 and the cleaning media usually cost £1-2 per litre.
Can extend the lifetime of metal tools and furniture by allowing them to be easily refinished.
Is portable so can be used in virtually any location.
Cons?
The abrasive media can damage delicate objects.
This cleaning process cannot remove contaminating grease.
Cannot clean internal chambers or small holes where the jet cannot reach.
Comparisons:
More abrasive than ultrasonic cleaning
Messier than blast cleaning with water.
May require a further clean to remove the blast media
[4]https://www.popularmechanics.com/cars/how-to/a9462/how-to-blast-your-car-parts-clean-15997905/
Chemical Cleaning or Soaking
What is it?
Chemical cleaning is a method used to get rid of contaminants from the surface of equipment including kettles, heat exchangers, pipelines and tanks. It is also a method used to decontaminate, disinfect and purify contaminated water.
How does it work?
Depending on the object and contaminant, a specific chemical can be used to remove the contaminant by dissolving it from the object. For example, an acidic solution can help to break down and remove limescale. In some situations, chemical cleaning is combined with a mechanical cleaning method such as ultrasonic cleaning in order to optimise the cleaning process.
What can it clean?
Chemical cleaning can be used for; limescale removal and prevention; Biofilm removal, legionella disinfection, surface disinfection, suture activation with UV radiation, ozone disinfection, surface corrosion treatment, scent removal off of walls and pipes and corrosion prevention CV-pipes, aluminium silos and various metal systems.
Pros?
Can effectively remove tough or bonded contaminants.
The process is generally fairly cheap as long as the chemicals used are uncomplicated and not dangerous.
Can easily clean internal chambers and anywhere the chemical can reach.
Cons?
Produces potentially dangerous contaminated waste fluid and some reactions can create toxic gasses.
If the chemical is not chosen carefully it may corrode the object being cleaned or the tank the cleaning is taking place in.
May require additional cleaning processes to clean the cleaning chemical from the object after the process.
Since only a chemical process is involved, it often involves more aggressive chemicals than a hybrid system employing both chemical and physical cleaning actions.
Comparisons:
Potentially more potentially damaging than ultrasonic cleaning, depending on the chemical required.
Usually produces less waste fluid than blast cleaning with liquids.
[5] https://www.hubbardhall.com/applications/surface-cleaning/copper-cleaning/
Electro-cleaning
What is it?
Electro-cleaning is when an electric current is applied to a bath which has been filled with a cleaning solution that acts as an electrolyte, causing any objects in the bath to be vigorously cleaned by removing their surface and transferring it through the solution to the oppositely charged item.
How does it work?
There are two types of electro-cleaning, reverse current (anodic) and direct current (cathodic). There is also a combination electro-cleaning which periodically switches between the two.
Reverse current electro-cleaning involves the metal being cleaned acting as an anode, the metal surface will both be cleaned and dissolved in this process with oxygen released where the metal meets the cleaning solution. Anodic cleaning is done in an alkaline cleaning solution and cannot be used on aluminium, chromium, magnesium or brass as these would produce a difficult to remove residue. The dissolved material from the anode attaches to the cathode due to the electric charges of the anode, cathode and ions of contaminant produced in the chemical reactions occurring on the surface of the anode, this means that the anode can be effectively cleaned.
Direct current electro-cleaning involves the metal being cleaning acting as a cathode, the cleaning process produces hydrogen gas bubbles at the boundary between the cleaning solution and the metal. Ions produced in chemical reactions occurring on the surface of the positively charged anode are attracted to the negative cathode, they effectively plate it with a new layer of ‘clean’ material.
The specific conditions (solution used, size of tank, time taken, temperature, current etc.) are dependent on the material being cleaned and the contaminant being removed from it.
What can it clean?
It is commonly used to prepared metal surfaces for electroplating but it can also be used for the removal of soil, grease and corrosive elements from almost any metal surface.
Pros?
This method is generally cheap.
The metal object is not damaged or significantly changed in the process.
The whole surface of the object including holes and grooves can be cleaned.
Cons?
Can only be used to clean metals.
Produces another piece of metal that has either been sacrificed (stripped) in cathodic cleaning or a piece of metal coated with the material cleaned from the anode in anodic cleaning.
Requires expertise in electronics and chemistry so cannot be carried out by untrained operators.
Comparisons:
Produces less waste than blast cleaning.
Can clean a smaller range of objects than ultrasonic cleaning.
[6] https://www.sharrettsplating.com/blog/what-is-electrocleaning/
[7] https://www.goldplating.com/blogs/news/electrocleaning-methods
[8] https://www.pfonline.com/articles/better-electrocleaning
If you need any help determining the best cleaning method for your circumstances please just get in touch and we’ll be happy to help. Call us today on 01924 495 975 or email hello@sonicsolutionsltd.com