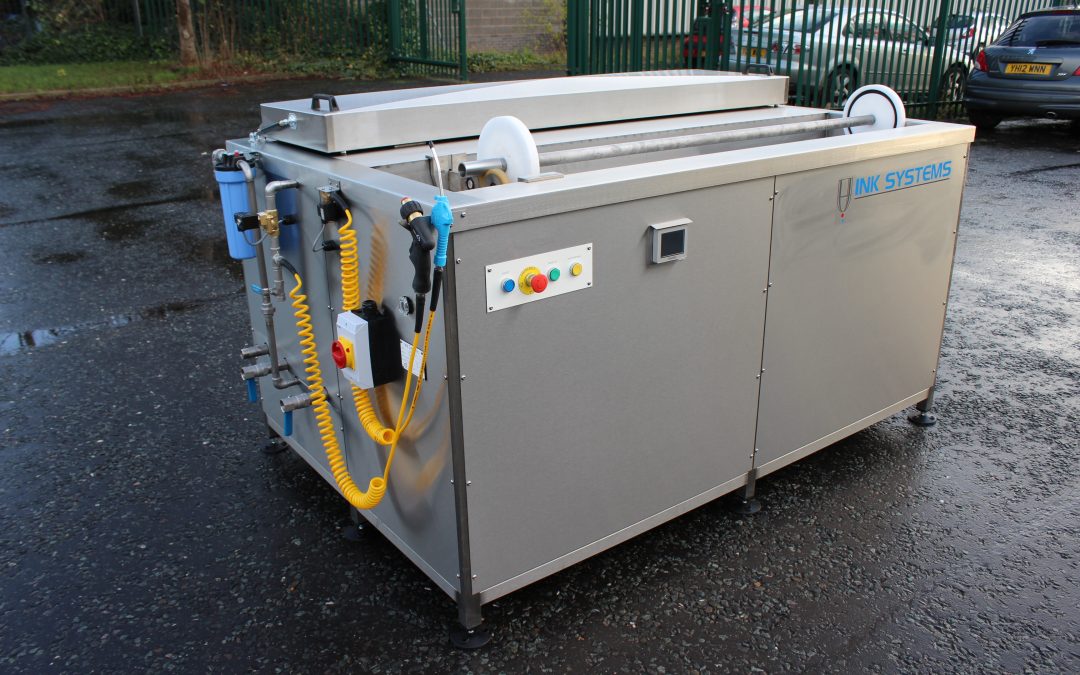
In this blog post we literally take a deep dive into the various elements that make up an ultrasonic cleaning bath. We cover everything from the components of the bath itself, right through to the cleaning solutions we use so hopefully this gives you some insight into the equipment we utilise to get things so clean!
How Does an Ultrasonic Cleaning Machine Work?
An ultrasonic cleaning machine is simply a bath filled with a cleaning solution through which ultrasound is passed. Items placed within the bath will be subjected to the ultrasonic cleaning activity, specifically the implosions caused by cavitation which sucks dirt off the surface of items placed within the bath.
An ultrasonic cleaning bath typically has 5 components;
The bath itself, to hold the cleaning solution and the parts being cleaned. Size does matter! The bath must be large enough to hold the basket with parts being cleaned, with sufficient space for an effective clean.
The cleaning solution used to remove the dirt of items placed in the bath. The cleaning solution must assist in taking the dirt off, not damage the item being cleaned, and effectively transmit ultrasonic waves. Health, safety and environmental factors regarding the handling, storage and disposal of the solution are also important considerations.
A basket to hold the parts being cleaned in the bath. The basket holds the items being cleaned off the base of the tank, and does not impede ultrasonic activity. It must clearly be strong enough and with a mesh of the right size to hold the items being cleaned securely and safely during the cleaning process.
A generator that converts mains frequency (50 Hz in the UK) to an ultrasonic frequency typically 25 to 80 kHz
This is often sited away from the bath itself for safety and ease of maintenance.
Transducers that vibrate at the frequency generated by the generator transmitting the ultrasound waves through the solution within the bath. These transducers are designed to vibrate effectively at the frequency produced by the generator. They can be sited on the base or walls of the bath itself, using the steel walls as the diaphragm to pass the waves through the solution inside the bath. Alternatively, the transducers can be bonded on the inside walls of a steel box which is submerged in the bath. The ultrasound waves are then passed from the “submersible” into the bath solution. For larger baths, submersibles are often preferred to tank bonded transducers since they are easier to remove for maintenance separately from the bath itself.
Although the general set up of an ultrasonic cleaner is the same, the specific details of the components are variable depending on the exact cleaning process it is designed for.
The Basket
The object being cleaned must be securely suspended several centimetres above the base of the tank and away from the tank sides. This can be achieved using a metal basket (as shown below) either suspended from the top of the tank sides or supported by rubber-coated feet positioned near the corners of the tank floor. This is done in order to prevent the object, or the basket/shelf holding it, from damaging the transducers which are fitted to the floor (or walls) of the tank as they can corrode the tank/transducers when the cavitation bubbles make them vibrate. This also ensures that there is sufficient room for the ultrasound waves to travel through the tank and remain undamped.
Alternatively, objects being cleaned can be suspended in the cleaning solution on shelves fixed to the sides of the tank (when the transducers are located on the floor of the tank).
The type of basket used can also affect the ultrasonic activity depending on the thickness of the mesh, the material it is made of and the total weight of the basket. This is a complete study in itself, since the effect of the basket upon ultrasonic activity is inter-dependent with other factors such as frequency, temperature, chemistry, contamination type and levels, and the size and geometry of items being cleaned.
A metal basket will absorb energy from the ultrasonic waves in the cleaning solution However metal is still considered to be the best basket material due to its strength, resistance to chemicals and ability to withstand high temperatures. The best advice is usually to make sure the basket is strong enough and secure enough for the parts being cleaned, whilst keeping the mesh thickness and weft to a sensible level. Any improvements to the cleaning performance can then be achieved through modifying the chemistry, temperature, cycle time and ultrasonic power.
The Bath
The cleaning bath contains and protects the components of the cleaning process. As such it must be large enough to fit in the basket and objects to be cleaned with enough free space for the ultrasound waves to propagate (travel) freely without damping. As a rule, the weight of the water should be double that of the objects to be cleaned.
Good quality cleaning tanks are made of high-grade stainless steel (316L is commonly used) which is suitably resistant to erosion damage from cavitation and corrosion from cleaning solutions. The thickness of this tank should be a minimum of 1.6mm to ensure durability and resistance to both ultrasonic erosion and chemical corrosion. Baths made of lighter, lower grade material, will not be as durable or effective, although maybe adequate for lighter, occasional use.
These tanks are compatible with the majority of waterbased cleaning solutions although strongly acidic solutions can still corrode the stainless steel tank. To overcome this a separation between acidic cleaning solutions and the tank should be maintained, for example with an acid-resistant tub within the metal tank with a secure lid.
A thermostat should be fitted to the bath in order to monitor and control the temperature to maintain/achieve optimum cleaning conditions for the specific solution being used and the item being cleaned. The thermostat should be made and fitted so as to ensure it isn’t damaged by the ultrasonic waves and cavitation bubbles in the bath. Additional measuring devices, such as pH and conductivity sensors can be used to maintain and to determine the optimum conditions for ultrasonic cleaning.
Timing controls to govern the ultrasonic cycle time are also typically used to allow operators to complete other tasks during a clean without risking leaving items in active ultrasonics for too long. Often such options can be incorporated into a plc control unit enabling the operative to select the correct process for the task in hand.
The Cleaning Solution
The ideal ultrasonic cleaning solution must do 3 things:
- Remove, or assist in removing the contaminant;
- It must NOT damage the item being cleaned;
- It must allow the free movement and propagation of ultrasonic waves and cavitation.
Additional qualities desirable in a solution used in an ultrasonic cleaning process include its ability to “wet” all the surface of items to be cleaned; to hold and maximise the volume of contaminant removed in the solution; to prevent mineral content in the water itself from interfering with the ultrasonics and the cleaning process. To achieve these lesser, but still important aspects of cleaning, most ultrasonic cleaning chemicals will also contain surfactants (normally anionic), chelants, detergents, wetting agents, and solvents. The chemistry of the cleaning solution used in an ultrasonic tank is a complete study in itself and considered in greater depth in future blogs we shall be putting out.
Depending upon the contaminant to be removed a wide variety of solutions are used to assist in the removal of the contaminant(s) by increasing its solubility and by breaking it down. The chemistry of the cleaning solution is as important as the physical ultrasonic cleaning action. In some instances, an inhibitor can be added to a cleaning solution to prevent it from corroding or otherwise damaging the object being cleaned. This is often used in, for example, the use of highly acidic and alkaline solutions to clean lighter metals like aluminium.
Substances that are viscous tend to introduce air into the solution and substances that are not totally water-miscible are also not good cleaning solutions in an ultrasonic application. This is because increased air content inhibits cavitation; increased viscosity causes the ultrasound waves to be damped reducing the power of the cavitation and substances must mix well with water in order to be less dense and less viscous.
There are a large number of cleaning chemicals available, depending upon the contamination to be removed. Future blogs will address cleaning solutions in specific applications, but the 3 primary functions mentioned above are as good a place to start as any.
The Generator
An ultrasonic generator is needed in all ultrasonic cleaning systems to provide the electrical energy at the chosen frequency(ies) to power the transducers in the ultrasonic cleaning system. The generator receives and converts the energy from the external power source to have the frequency and voltage required for optimal cleaning. Mains electricity in the UK is supplied at a voltage of 230 V and at a frequency of 50 Hz, but these are not the required values for optimised ultrasonic cleaning, so the generator is needed to convert these values to the desired ones. The optimum voltage is usually higher than the voltage of the mains electricity supply and the optimum frequency is generally within the range 20 kHz to 80kHz.
Technological advances in modern ultrasonic cleaners mean that some generators can obtain feedback from the transducers, allowing them to adjust their output to maintain optimal cleaning. In certain situations, generators can be adjusted to produce variations in the ultrasounds waveform in order to optimise the cleaning quality without damaging the objects being cleaned. This is often referred to as a sweep function, which varies the actual frequency being generated in a band of 1-2kHz around the average frequency desired. This prevents the build-up of “hot” and “cold” spots of standing waves in either a compressed or rarefied state, which could lead to damage to the item being cleaned or lack of cavitation and cleaning.
The Transducers
Transducers are devices that convert energy input from one system and produce another form of energy in a second system. In the case of ultrasonic cleaning, an oscillatory transducer generates ultrasonic sound waves in the second system (inside the tank) from an alternating electrical current which is provided by the generator.
Transducers are usually either bonded to the walls or floor of the tank or suspended within the cleaning solution in a submersible case. An array of transducers is used in the bath to ensure that ultrasound waves are produced across the whole volume of the bath in order to produce effective cleaning.
In the production of longitudinal waves by the transducers, electrical power is supplied to drive a vibrating component or ‘diaphragm’. The transducers used in ultrasonic cleaning are defined as actuators, which are devices which control or move a mechanical system in response to signals from a control system, and are driven by a source of energy (in this case an electrical current). Most transducers used in ultrasonic cleaning applications are piezoelectric, in which the active element (piezoelectric crystals) increases and decreases in size with the fluctuations of the alternating current supply (an alternating current supply rapidly switches between positive and negative current). A diagram of a piezoelectric transducer is shown in the figure below.
Characteristics of piezoelectric transducers which make them ideal for use in ultrasonic cleaning include their flexibility (ability to be moulded into different sizes and shaped), small dimensions and large measuring range which make them easy to install and use. Also, piezoelectric transducers have a particularly high-frequency response, meaning that their parameters change quickly with changing conditions/input. Their relatively low cost is also a considerable advantage!
Piezoelectric transducers are also used in quartz watches to keep the time perfectly precise and in WWI, the echoing of pressure/sound waves from piezoelectric transducers were used to detect enemy ships using sonar.
For a free trial clean, a no-obligation discussion, or even a visit when the current situation permits, just call us on 01924 495 975 or e-mail Andrew on andrew@sonicsolutionsltd.com