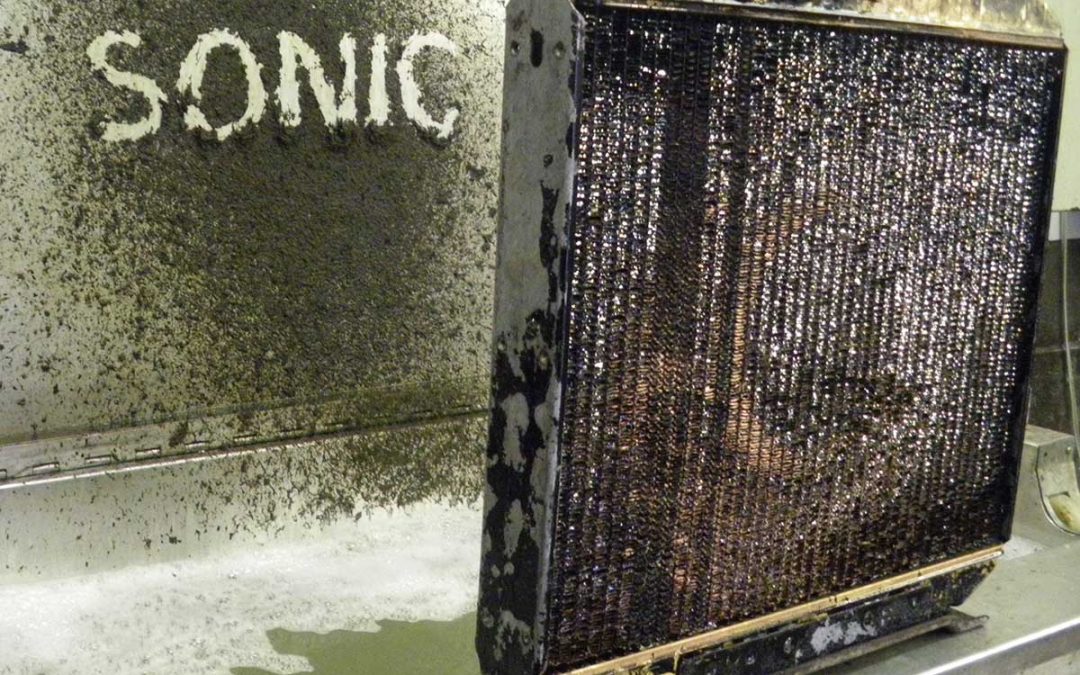
Cleaning parts is free!
When you consider the true costs of dirt on either the end product or the parts used to make the end product, the removal of that dirt is free. It costs much less to remove the dirt than to leave it on and suffer the consequences. The true costs of leaving dirt on include the following;
- Rework – often by skilled personnel, and using additional materials;
- Scrapping of product and material – often of material whose only defect is dirt;
- Repeated service – when failure due to dirt requires replacement parts or service both time and material is wasted;
- Inspection – “inspecting out” dirt is rarely cheap !
- Testing – where the consequences of dirt requires intense testing of parts prior to dispatch;
- Delay and failure to meet schedules – where dirt requires rework it is often the case that production schedules fall behind with consequent costs of failure to meet orders and customer timetables;
- Warranty costs – the direct costs of replacement or repair plus the often significant damage to reputation.
Over the 15 plus years we have been cleaning industrial parts the most commonly cited reasons (with statistics often quoted) for getting us in to either do the cleaning or to supply the cleaning equipment and process, have been as follows;
Time taken in house to do the cleaning, often by skilled personnel, often done badly, and usually very unpopular with staff ! The direct cost of this Labour and the opportunity cost of lost production was calculated at around 7.6% of total production time by an electronics company, a truly staggering amount.
Scrap from wasted product – one printing company cited scrap paper and ink from dirty production parts was running at 1% of total material cost. in this case 1% of many millions of pounds. Another company making electronic sensors estimated product failure costs attributable to dirt were running at 2% on items worth many thousands of pounds each.
Production downtime and process failure – when a line or process has to be stopped because of dirt, the outcome ranges from costly inconvenience to near total disaster. One instance of the latter is when a power station brought dirty filters that had resulted in the power generating turbines stopping completely. Now matters are rarely as extreme as this, but stopped production lines not only occupy expensive labour to put right but result in either lost production or delayed production. The costs of both can be very high.
Delays – Time is money and, whilst similar to the above, the cost of delays to production or despatch are often overlooked but considerable. In an increasingly “just in time” world if a product is not available when needed the consequences are potentially serious. Lost sales, reputational damage, poor on-line ratings and disrupted process flows are the costs associated with delays and over time can destroy businesses. Many businesses, particularly B2C, have found delay getting product to market near fatal. One automotive parts customer calculated lost sales because customers were sourcing parts from competitors when they experienced delays from themselves as up to 3% of sales. The majority of delays were caused by product rejection, a principal cause of which was dirty product.
Health, Safety & Environmental – Dirt itself can be a hazard to either the product or personnel. This is most noticeable in areas such as food, pharmaceutical and medical, where dirt can threaten lives. However even when not taken to this extent, a product contaminated with dirt is a diminished, less valuable product. If a competitor is offering a similar product without this, they will appear superior.
To book a Free Trial Clean or to discuss your ultrasonic cleaning requirements with one of our expert staff. Call us today on 01924 495 975 or email hello@sonicsolutionsltd.com