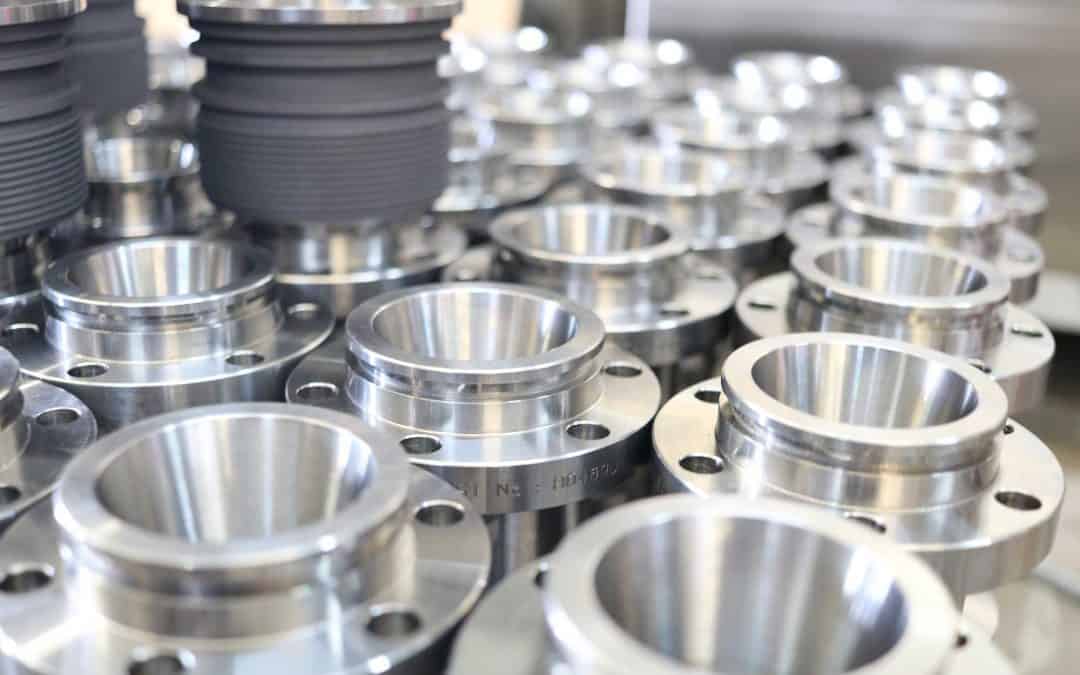
If you are undertaking a new project that requires parts to be ultrasonically cleaned, a question you may ask is:
Should we undertake the cleaning ourselves or outsource it?
To decide which option is better for your business, there are several points that you should consider.
What volumes are you expecting to clean?
If you are only expecting a small volume of parts to need cleaning then it would be easier to outsource the cleaning work. Even a small industrial ultrasonic tank will cost upwards of £2000. If you only have 500 items that a cleaning company such as ourselves can clean for £1 per item, it makes much more financial sense to outsource.
Is the project ongoing?
This ties in with the volumes. Are you going to be producing a certain volume of parts per month indefinitely? Or is it just a few parts whenever they are ordered?
If you have a full production schedule where you know you will require ultrasonic cleaning for a given length of time, then it is a good idea to look into purchasing your own equipment.
How much budget do you have?
As I have already said, ultrasonic baths can be very expensive, especially if you are looking to clean large items. If you are working on a multi-million pound project then cost may not be an issue. But for most, a £50,000 investment in machinery cannot be taken lightly. Before you even consider purchasing your own ultrasonic bath, you should take a detailed look at your budget and see how much capital you have to work with. And yes, you can pick up a cheap 5 litre tank from amazon, but they are not designed for industrial use and will not be able to handle volume work.
Have you considered the additional costs?
As well as the initial expense of the tank, there are also the running costs that have to be considered.
Cleaning solution – The chemical that is added to the tank.
Power – The energy required to use the tank.
Waste disposal – The correct disposal of your waste solution.
Do you have the right personnel?
Are you going to have a dedicated member of staff to operate the tank or are your existing production staff going to take on the roll? Whatever you decide, you must ensure that whoever is operating the machine has adequate training to get the best results from it.
Other things to consider are the amenities needed for your own tank.
Do you have enough free floor space?
Do you have a water and power supply?
Is there adequate ventilation?
Have you considered health and safety factors?
When operating an ultrasonic tank, PPE must be worn to protect the operator from accidents. This is usually gloves, goggles, and an overall but some chemicals require a mask to be worn too. Wherever an ultrasonic tank is situated on a company’s premises they need to have a dedicated area where PPE must be worn beyond a certain point.
Do you just need it for one job?
If you are only producing one part that needs to be ultrasonically cleaned out of a large product range then you have to consider whether the machine is going to be used enough to warrant buying one. That said, once you have your own tank, it’s easy to find things that could do with an ultrasonic spruce up.
So when DOES it make sense to get your own machine?
We get a lot of enquiries from people looking into getting their own tank and around 80% of them are put off once they hear the cost of the tank they require. Unless you are cleaning volumes of parts on a regular basis, then it is best to leave it to the professionals and use an outsourced company like ourselves.
If your production is time-sensitive and you want to stay in control of the entire process then it makes sense to keep the cleaning in house. The logistics of sending out parts to a third party can add days to a production schedule and for some this is just not viable.
For a free trial clean, a no-obligation discussion, or even a visit when the current situation permits, just call us on 01924 495 975 or e-mail Toby on toby@sonicsolutionsltd.com